As production for the first Bentley Mulsanne exemplars is about to start, the British manufacturer has offered extra information regarding the manual work required to create the luxurious environment that every Mulsanne will offer.
The company is well known for the ultra-rigorous approach to quality, and to give you an example, every new leather and wood veneer option has undergone numerous tests involving extreme temperatures and various durability tests. To make sure the leather inside the new Bentley Mulsanne will not stain or fade, the company has applied samples of sun creams, skin lotions and even artificial human perspiration, making sure everything will be perfect.
This is just one small stage in the whole Bentley Mulsanne craftsmanship process for which you will find extensive details in the official press release below.
Bentley press release :
(Crewe, England) When Bentley’s craftsmen and women begin this summer to create the very first production examples of the new Mulsanne’s beautiful cabin, it will represent the culmination of an extraordinary four-year journey for the Crewe-based company. While Bentley is long renowned for its handcrafted interiors, it was decided at the earliest stages of concept planning that even higher standards of quality and luxury would be required for the new Mulsanne, the company’s new flagship Grand Tourer.
Bentley’s Design team, led by Dirk van Braeckel, commissioned an exhaustive research study to identify the classic signature features that have defined Bentleys from the 1920s to the present day, as Dirk explains:
“Hundreds of cars were the subject of a painstaking review to define highly challenging targets for every facet of the new Mulsanne’s interior. This embraced key elements, such as materials, colour harmony and craftsmanship, ensuring the new Mulsanne will become the purest expression of Bentley design yet.”
Similarly stringent targets were set for the operational refinement and robustness of all control mechanisms to provide Crewe’s craftsmen and women with materials and components of the highest quality and authenticity.
Responding to customer demand, the research study even extended to the smell of the leather hides. This resulted in the reintroduction of a complex, traditional tanning process to create a rich, mature leather aroma, evoking that of vintage Bentleys.
When production begins later this year, Mulsanne customers may select from a broad palette of hides, including a range of 24 ‘standard’ colours as well as a wide selection of rich ‘heritage’ colours from previous Bentley models. These colours may be specified in single-tone or duo-tone combinations in four different styles (colour splits) allowing the customer to choose not just the colour scheme but also the mood of the interior – from very elegant to sporty.
These exquisite hides are fashioned by a team of craftsmen and women who apply the same fastidious attention to every detail of the opulent cabin. All stowage compartments, including iPod drawer, glovebox and luggage compartment are leather-lined, while the creation of the hand-sewn leather rim around the Mulsanne’s steering wheel takes two days of intense, expert concentration – even longer if the customer opts for cross-stitching.
Bentley’s unrivalled expertise in the crafting of leather is complemented by the extraordinary skills of the company’s ‘Wood Shop’, the largest of its kind in the luxury car industry.
It takes five weeks to turn a rough ‘root ball’ (individually selected by Bentley experts) into a full set of mirror-matched, fine-polished leaves. Each piece of veneer is carefully stored in a special humidity-controlled chamber and then applied onto a solid walnut base, a process that alone takes two weeks to complete. Veneers are then polished to a perfect mirror finish. The quality of every piece is carefully inspected and approved before being delivered to the vehicle assembly hall.
The entire Mulsanne cabin is encased by a ‘ring of wood’ waistrail, as part of which a single, ‘unbroken’ panel of wood graces the Mulsanne’s dashboard. Customers may select from an extensive range of premium quality veneers, unbleached for a natural appearance, including Walnut, Piano Black, Oak, Bird’s Eye Maple, Vavona, Olive Ash and Sapelli Pommele, harvested from sustainable sources across the globe.
Utilising the intricate skills of the Crewe-based experts, two marquetry options are available for the new Mulsanne: picture framing-style inlays to waistrails and contemporary-style crossbanding and inlay to dashboard and waistrails.
One of the most striking examples of Bentley craft skills can be found on the Mulsanne’s upper dashboard where a new 8-inch multimedia screen is housed unobtrusively behind an electrically operated veneered door. When the screen is not required the door blends effortlessly into the veneered dashboard.
The exquisite hides and veneers of Bentley’s new flagship are fashioned by the company’s highly skilled craftsmen and women with over 40 years’ experience who will invest over 170 hours into creating the interior of just one Mulsanne, as Robin Page, Head of Interior Design, comments:
“Crafting the Mulsanne’s interior represents a substantial part of the build process. At Crewe, Bentley’s way of working is the exact opposite of mass production – we start where others stop.”
The ‘starting where others stop’ philosophy has been applied to virtually every feature of the Mulsanne’s cabin. The use of wood and leather hides has been significantly increased for an even more refined and sumptuous cabin, while the stainless steel brightware receives an intensive 10-hour finishing process to offer a near-perfect gleam (ensuring that even the smallest part will catch the eye). The carpet has been given increased fibre depth and density to further enhance the quality feel.
An ultra-rigorous approach to quality, applied from the earliest planning stages, means that the Mulsanne’s interior will be enjoyed by current as well as future generations of drivers. Every new leather and wood veneer option was subjected to extreme temperatures as well as an exhaustive array of further durability tests. Sun creams, skin lotions and even a chemical formula for human perspiration were applied to leather hide samples to ensure no staining or fading.
And perhaps most remarkably, the durability of a hide will be is tested over 20,000 times by a team of people of varying height and weight (rather than the robots used by other manufacturers) to provide the most authentic, real-world assessment possible.
“Much of our work takes place behind the scenes,” explains John Minshull, Head of the Bentley Laboratory at Crewe.
“However, this development and scientific testing work is a key part of the Mulsanne story as it provides our craftsmen and women with the best quality materials. And it is the combination of their creativity and our research which makes the Mulsanne interior so special.”
Bentley Mulsanne Craftsmanship Video :
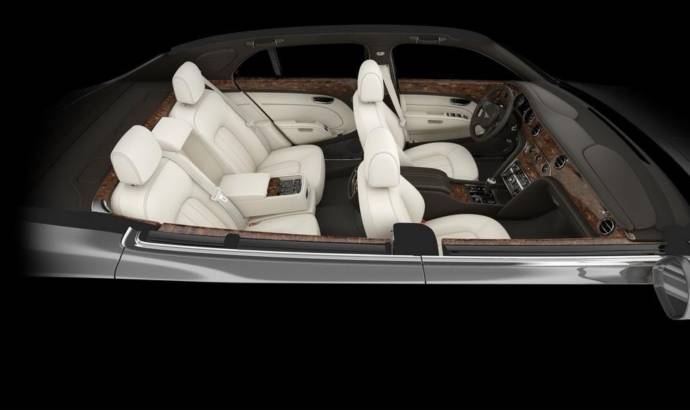
15 Apr 2010
0